Learning & Adaptive Mechatronic Systems
The four central requirements for industrial automation components are short commissioning time, high precision, reliability, and resource-efficient operation over a component’s entire lifetime. To meet these demands, we develop estimation and control algorithms for mechatronic systems. These algorithms enable system configurability and adaptability to constantly changing operating conditions. This requires precise and easy-to-apply modelling and verification techniques, as well as adaptive and learning control algorithms to impose the desired behaviour on the system. We aim at simplifying variant configuration, mitigating control performance degradation due to manufacturing tolerances and aging, and extending the life span of mechatronic automation components.
Fields of application:
Manufacturers of automation components

Mechatronic Design
Mechatronic system design is the integrated design of a mechanical and electronic system and its embedded control system. Our mechatronic design methodology consists of five concurrent stages: modelling, algorithmic design, simulation, prototyping, and deployment. We assign design requirements to specific systems, subsystems, and components, and assist our clients in selecting, optimally placing, and integrating sensors and actuators for a given problem. We accomplished this by evaluating price, measurement or actuation principle, and accuracy.

Model-Based
Algorithm and Software Design
Model-based design is the mathematical answer to problems associated with designing complex control systems: a mathematical model captures all relevant system information and is used throughout the entire development process – design, simulation, implementation, and verification & validation. The model is continuously updated and evaluated. Concurrent realisation of real-time capability, computational efficiency, and robustness is achieved through the systematic use of rapid prototyping tools and relevant testing approaches. That is why model-based software design, represented by MiL, SiL or HiL, is an integral part of our daily research routine. Moreover, we exploit the link between system analysis and numerical simulations by applying stochastic approaches to verify the performance of highly complex nonlinear control loops, which becomes crucial when incorporating unknown operating conditions.

Control of Electric Drive Systems
Ranging from industrial plants to robotic applications and vehicles – electric drives are ubiquitous. Our research focus in this area lies with the optimal control of electric drive systems. This incorporates:
- Energy optimisation with motor-specific online-adapted MTPA strategies.
- Lifetime and maintenance optimisation by derating strategies.
- Costs decrease and robustness increase using virtual sensor concepts.
- EMC optimisation with adaptive VSI control.
- Start-up time optimisation by employing automated self-commissioning strategies.
- Control performance optimisation due to adaptive control algorithms.
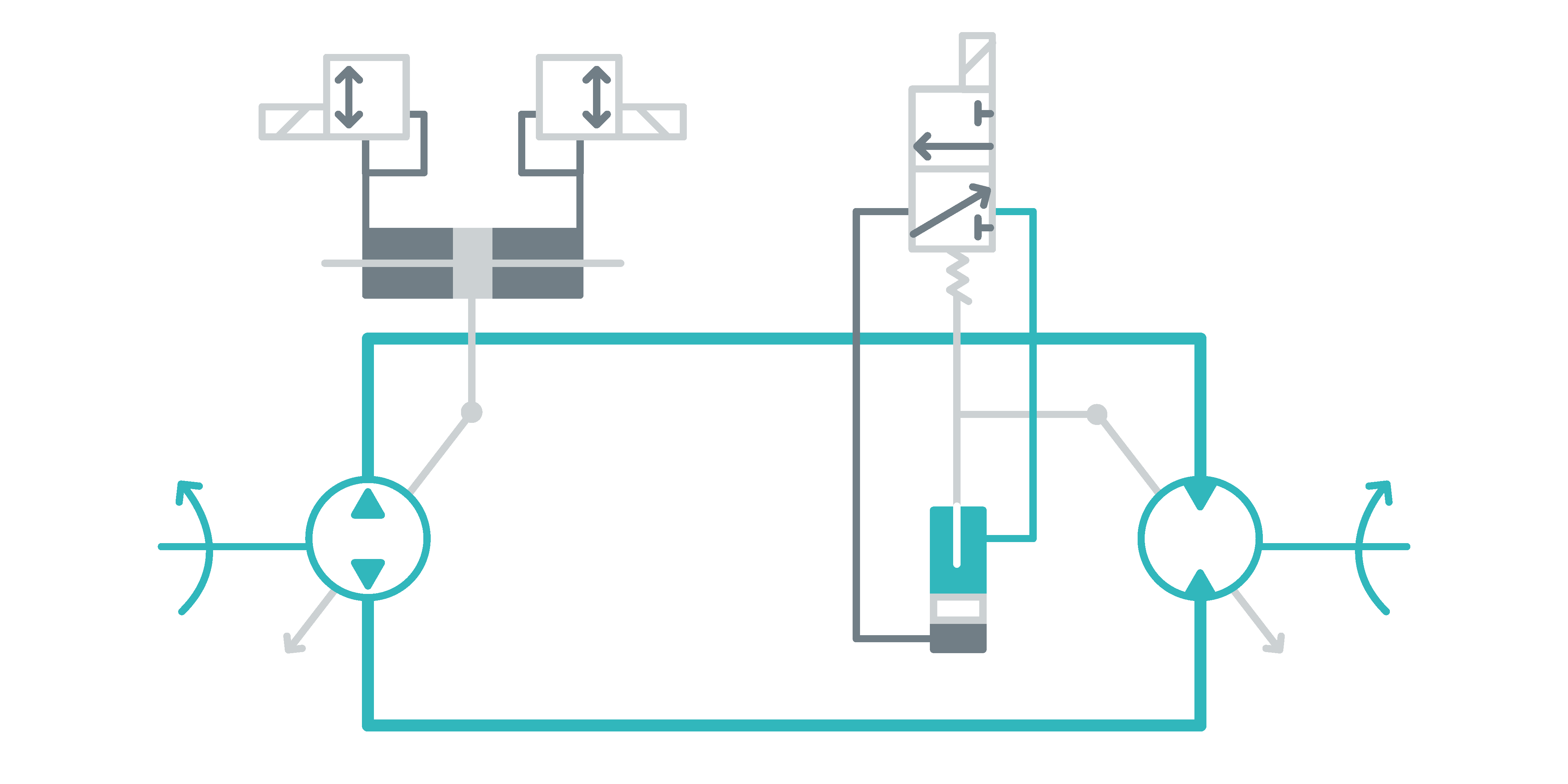
Controlling Pneumatic and Hydraulic Drive Components
Fluid power technology deals with the generation, control, and transmission of forces and the resulting movement of mechanical elements by pressurised fluids in a confined system. Unlike electric motors, hydraulic motors can produce a large amount of torque while requiring minimal installation space. We support our clients in construction and agriculture in designing mobile hydraulic control systems for high torque applications, such as tower cranes or excavators.
Pneumatic applications are relevant to factory automation in the automotive industry and many others. We therefore develop learning and adaptive control algorithms (position, force and compliance control) to mitigate performance deterioration due to aging effects and component tolerances and to enable automated recommissioning following downtimes. This allows our partners to employ the same controller within a class of structurally comparable systems and perform virtual reconfiguration of components.
Associated Research Topics
Research Groups Involved