Autonomous Work Machines
Unpredictable and difficult terrain, harsh weather conditions, collaboration with humans and other machines, and limited connectivity place high demands on robotic systems in outdoor environments. We develop intelligent functions and algorithms for work machines such as excavators, dump trucks, forklifts, or cranes for assistive or autonomous operation that meet these requirements.
We can work together with you to increase the efficiency, safety, and productivity of your work machines and thus counteract skilled labor shortages, reduce costs, and enable 24/7 operation. Using simulation tools, we minimize development and testing efforts, while detection, localization, and mapping ensure reliable navigation in changing terrain and weather conditions. Task and motion planning as well as drive control from our team provide the necessary precision and robustness in dynamic scenarios. In this way, autonomous work machines extend human capabilities, ensure high-quality work results, and strengthen competitiveness – a decisive response to the growing challenges of demographic change.
As your research partner, we offer you:
- Development of autonomous systems: We support you in the conception, implementation, and integration of intelligent assistance functions and fully autonomous machines.
- Requirements analyses and feasibility studies: Through workshops and thorough investigations, we ensure that your project is technically feasible and offers sustainable added value.
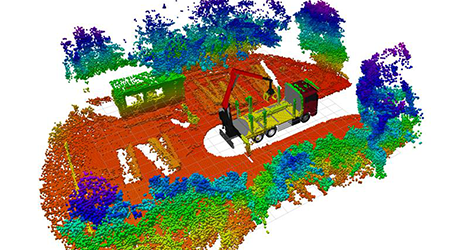
Detection,
Localization
& Mapping
Unlike controlled indoor environments, autonomous work machines operating outdoors face variable conditions such as unstructured and dynamic surroundings and complex traffic situations involving both humans and machines. The selection and integration of required sensors and appropriate algorithms to develop perceptive capabilities forms the foundation for safety in human-machine contexts and enables robust autonomous decision-making processes.
We develop reliable and powerful perception systems specifically designed for demanding outdoor conditions. Through methods of data fusion, context-based selection processes, and innovative sensor technologies, we achieve robust environmental detection and precise self-localization even in conditions with limited visibility. Our systems understand and interpret the structure and context of a scene to make intelligent decisions.
We combine advanced sensors with powerful algorithms to equip your work machines with precise and reliable perception capabilities – the foundation for safe autonomy in real-world applications.
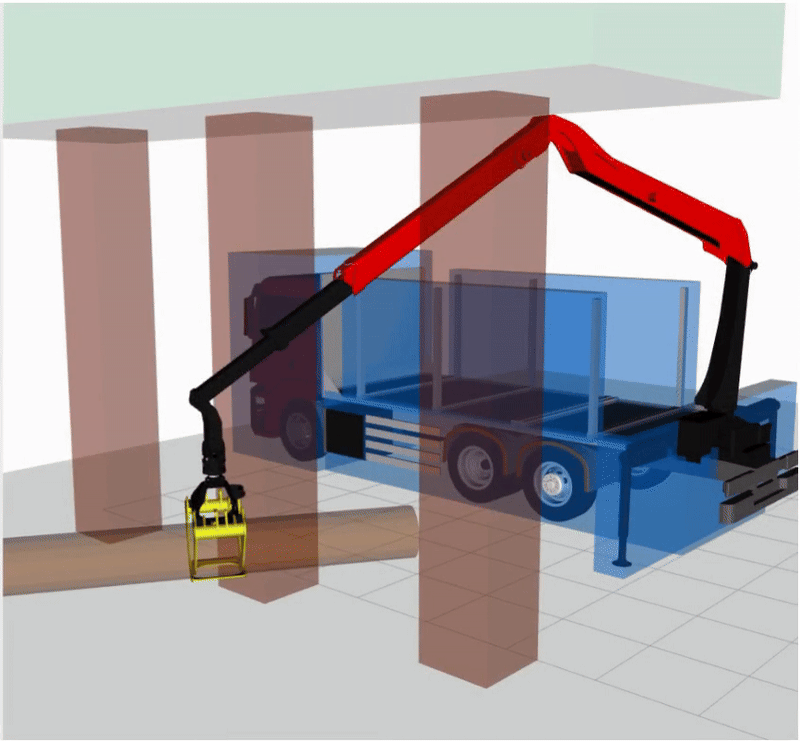
Control,
Planning&
Decision Making
Work machines are used in dynamically changing and unstructured environments, where collisions can lead to significant property damage and personal injury. Therefore, their manual operation requires years of experience and great care.
We develop, integrate, and test assistance functions up to fully autonomous operation of your work machines to implement tasks effectively, robustly, and safely. Working in conjunction with our perception systems, we recognize and process changes in the environment and adapt task and motion planning at runtime for collision avoidance and efficiency. With learning control algorithms, we achieve maximum precision even with system changes such as load fluctuations, wear, or aging.
We combine adaptive drive controls, dynamic perception, and intelligent planning methods to implement the right actions at the right time.
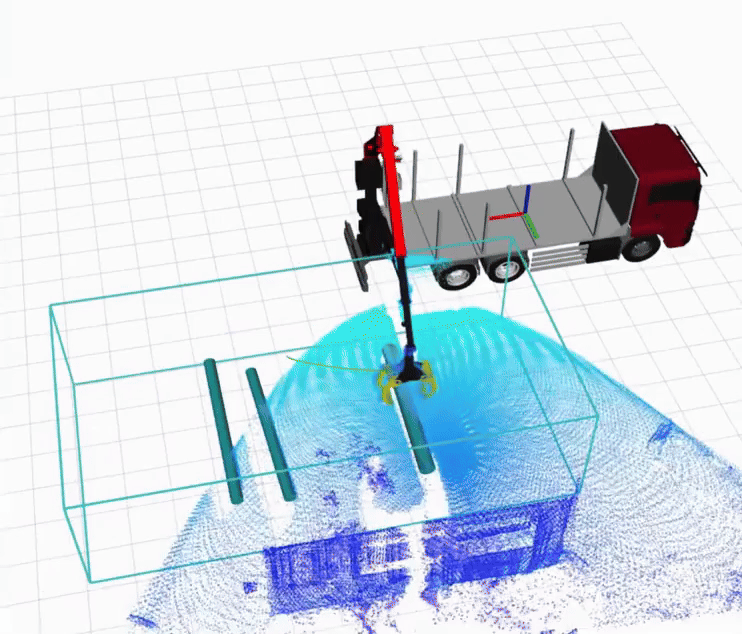
Modelling & Simulation
Direct prototype validation and verification presents numerous challenges and is not only costly and time-consuming but also carries substantial risks. Therefore, simulative validation and verification play a crucial role in our development process. Physically and visually realistic digital twins offer a valuable opportunity for operators to test future assistance functions in a virtual space.
We are able to replicate the dynamic behavior of the work machine as well as its interaction with the environment – whether rugged terrain, different weather conditions, or interaction with humans – in various realistic simulators. This allows potential problems to be identified and solved before deployment in the real world. To achieve this, we combine model-based and data-driven modeling with generative AI algorithms in a hybrid approach.
Our simulations enable a rapid innovation cycle, reduce costs and development time, and provide a safe testing environment. Additionally, we use digital twins as training simulators to optimally prepare operators for deployment.
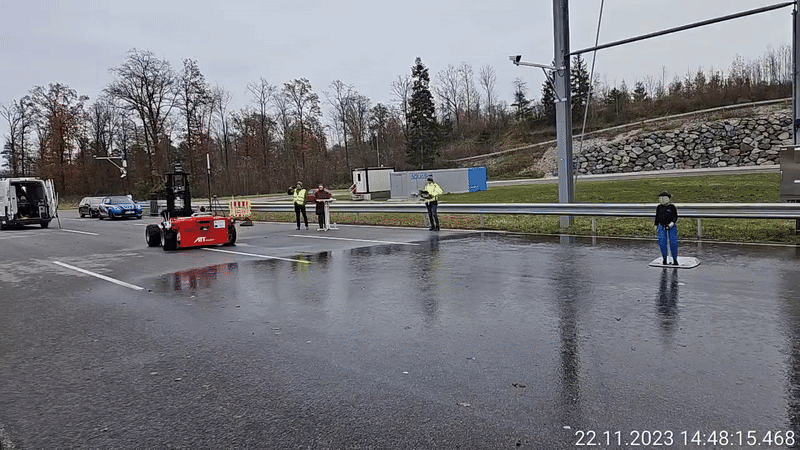
Safe & Reliable
Autonomous Systems
Robotic systems are subject to the highest safety and reliability requirements. System failures can cause significant costs, and malfunctions can lead to property damage or, in the worst case, accidents and personal injury during human-machine interactions. To prevent this, we place high demands on system design.
We develop system architectures that prioritize safety and combine complementary sensor technologies with intelligent sensor fusion algorithms. This, together with safety-oriented data analysis, enables reliable environmental perception – even under harsh environmental conditions. Our control concepts are designed to ensure reliability without compromising system efficiency. By using innovative verification and validation methods, we systematically test our algorithms under various disturbance scenarios and parameter uncertainties. In this way, we ensure a well-founded and statistically significant evaluation of our systems.
We integrate and develop robust, reliable monitoring systems that comply with the standards and regulations applicable to your use case. This is complemented by extensive system testing in both simulations and real operational scenarios.
Associated Research Topics
Research Groups Involved
Laboratories and Test Areas