Die Inline-Inspektion bei industriellen Prozessen, bei denen sich Teile kontinuierlich in einer Fertigungslinie bewegen, wird mehr und mehr zu einem unverzichtbaren Werkzeug für die industrielle Qualitätsprüfung. Forscher:innen des AIT setzen dies zum Beispiel bei Hochleistungsstahl-Erzeugnissen oder Banknoten um.
Moderne Produktionssysteme sind gekennzeichnet von hohen Geschwindigkeiten gepaart mit hohen Qualitätsansprüchen. Dies stellt höchste Anforderungen an die Qualitätskontrolle. Die wichtigste zerstörungsfreie Methode zur Inspektion ist die automatische Verarbeitung und Auswertung von Bildern, die mit Kameras direkt in der Produktion gemacht werden. Dabei kommen sowohl zweidimensionale als auch dreidimensionale Verfahren zur Anwendung; bei letzteren werden – ähnlich dem räumlichen Sehen bei uns Menschen – mehrere Bilder aus unterschiedlicher Kameraposition rechnerisch miteinander verknüpft.
An solchen modernen Methoden des „Inline Computational Imaging“ (ICI) arbeiten Forscher:innen am AIT Austrian Institute of Technology – Österreichs größter Research & Technology Organisation (RTO) – seit vielen Jahren. Entwickelt wurde beispielsweise ein Sensor, der eine simultane 2D- und 3D-Inspektion von bewegten Objekten ermöglicht. „In Kombination mit intelligenten Algorithmen ermöglicht die AIT-ICI-Technologie eine neue Dimension der schnellen und präzisen Inline-Inspektion. Wir können unseren Industriepartnern ganzheitliche Lösungen anbieten – das heißt von (optischen) Sensoren, die die Daten aufnehmen, bis hin zu Algorithmen, die z. B. selbständig entscheiden, ob es sich um einen Oberflächendefekt handelt oder nicht“, erläutert Andreas Vrabl, Leiter des AIT Centers for Vision, Automation & Control (VAC).
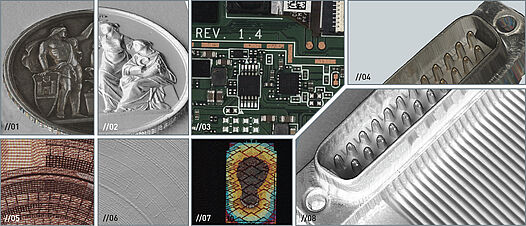
© AIT
Durch Methoden des Inline Computational Imaging können feinste Strukturen auf Oberflächen verschiedenster Gegenstände sichtbar gemacht und vermessen werden. Im Bild einige Anwendungsbeispiele: 3D Aufnahme mit Textur (01) und präzise 3D Rekonstruktion (02) einer Münze; All-in-focus Farbbild einer Leiterplatte (03); 3D-Aufnahme mit Textur (04) und präzise 3D Rekonstruktion (08) eines Steckers; Farbbild (05), Tiefdruck (06) und Hologramm (07) einer 10 Euro Banknote.
Moderne bildgebende Verfahren
Ein wichtiges Funktionsprinzip dahinter ist eine Kombination aus zwei verschiedenen bildgebenden Verfahren: Photometrie und Lichtfeld. Die Stereo-Photometrie verwendet Abbildungen des Objektes mit unterschiedlichen Beleuchtungsrichtungen: Sie berechnet aus den Schattierungsverläufen lokale Oberflächenkrümmungen und hat ihre Stärken in der Rekonstruktion von feinen Oberflächendetails wie Unebenheiten, Prägungen, Kratzer oder Poren. Die Lichtfeldtechnik hingegen verwendet Abbildungen aus verschiedenen Betrachtungswinkeln. Sie ist besonders gut in der Bestimmung des Höhenprofils für texturierte Bereiche, versagt jedoch bei Bereichen mit homogener oder glänzender Oberfläche sowie bei feinen Oberflächendetails.
Inline Computational Imaging kombiniert die beiden Methoden in einem kompakten Hardware-Setup. Der Sensorkopf besteht aus einer Matrixkamera und zwei oder mehr Lichtzeilen. Die Hardware ist fix installiert, während sich das Objekt auf einem Fließband unter der Kamera vorbei bewegt. Auf diese Weise ahmt ICI die Vorgehensweise eines Menschen nach, der beim Prüfen einer glänzenden Oberfläche die Betrachtungs- und Beleuchtungswinkel intuitiv variiert, um auch kleinste Defekte aufzuspüren.
Während sich das Objekt unter dem Sensor (Kamera und Beleuchtung) vorbeibewegt, wird die Beleuchtungsrichtung variiert und es werden kontinuierlich Bilder aufgenommen. Jede Einzelaufnahme bildet das Objekt dabei unter einem geringfügig anderen Betrachtungs- und Beleuchtungswinkel ab. „Die Kombination der beiden Methoden macht ICI weitgehend unabhängig von den Oberflächeneigenschaften der Prüfobjekte“, erklärt Markus Clabian, Head of Competence Unit High-Performance Vision Systems am AIT.
Prüfung von Edelstahl-Knüppeln
Ein gutes Beispiel dafür ist ein Kooperationsprojekt des AIT mit der voestalpine BÖHLER Edelstahl GmbH & Co KG. Diese stellt Hochleistungsstähle und Nickelbasislegierungen für die internationale Luftfahrt-, Automobil- sowie Öl- & Gasindustrie her. Ein Zwischenprodukt bei der Produktion von Edelstahlerzeugnissen sind sogenannte „Knüppel“ – diese haben einen quadratischen Querschnitt und werden zur weiteren Verarbeitung gewalzt. Für die Qualität der Endprodukte ist es entscheidend, dass die Walzknüppel an ihrer Oberfläche keine Fehler wie zum Beispiel Schlackeneinschlüsse oder Risse aufweisen. Diese würden sich beim Walzen vergrößern und die Eigenschaften der Endprodukte beeinträchtigen.
Wird ein derartiger Defekt an der Oberfläche erkannt, wird der Knüppel weiter geschliffen, bis die Oberfläche einwandfrei ist. Über die optimale Schleifbehandlung und die Zahl der nötigen Schleifdurchgänge entscheiden derzeit Mitarbeiter:innen, die die Oberfläche optisch nach Fehlern absuchen. „Nur wer ein geschultes Auge und langjährige Erfahrung hat, kann die Schlackeneinschlüsse erkennen oder feinste Risse im Stahl von Schleifspuren unterscheiden“, berichtet AIT-Forscherin Petra Thanner. Gemeinsam mit Expert:innen bei voestalpine Böhler Edelstahl in Kapfenberg wurde in den vergangenen Jahren an einem automatisierten Verfahren zum Aufspüren von Oberflächenfehlern bei Walzknüppeln gearbeitet. Verkompliziert wird die Aufgabe noch dadurch, dass die Knüppeloberflächen je nach Schleifbedingungen unterschiedlich gefärbt und gekrümmt sind, dass die Stahloberfläche stark glänzend sein kann (was Kamerabilder schwer auswertbar macht) und dass die Prüfung direkt in der rauen Produktionsumgebung des Walzwerkes durchgeführt werden muss. „An dieser Fülle an verschiedensten Herausforderungen ist in den vergangenen Jahren schon so mancher Versuch gescheitert, diesen zeitaufwendigen Prozess zu automatisieren“, berichtet Siegfried Kleber, Leiter der Verfahrensentwicklungsgruppe bei voestalpine Böhler Edelstahl.
Dennoch ist es nun gelungen, ein innovatives Prüfverfahren zu entwickeln und zur Industriereife zu bringen. Dabei ist eine Kamera fix über einem Prüfgegenstand installiert, der sich darunter bewegt. Beleuchtet wird die Szene aus vier verschiedenen Richtungen; diese sind so gewählt, dass der Unterschied zwischen Rissen und normalen Schleifspuren möglichst klar hervortritt. Die rohen Kamerabilder, auf denen die Defekte jeweils unterschiedliche Schattenwirkungen haben, werden im nächsten Schritt mithilfe von Photometrie-Verfahren weiterverarbeitet: Dabei wird zusätzlich zu detaillierten und kontrastreichen 2D-Bildern auch ein exaktes 3D-Modell der Oberfläche berechnet, in dem sich Oberflächendefekte noch deutlicher abzeichnen.
Künstliche Intelligenz erkennt Risse
Um diese Strukturen nun entweder als normale Schleifriefen oder als Fehler einzustufen, kommen Methoden der Künstlichen Intelligenz (KI) zum Einsatz: Ein künstliches Neuronales Netz wurde mit unzähligen Kamerabildern trainiert, bei denen zuvor händisch gekennzeichnet wurde, um welche Art von Oberflächenstruktur es sich handelt. Das KI-System lernte, unerwünschte Defekte sicher zu erkennen und in den Kamerabildern farblich zu kennzeichnen. „Der Hauptvorteil unseres Systems liegt darin, dass das bewegte Objekt mit nur einer Kamera unter mehreren Betrachtungswinkeln aufgenommen und diese Daten intelligent verknüpft werden“, fasst Markus Clabian zusammen.
Das vom AIT entwickelte Prüfsystem ist mittlerweile als Pilotanlage bei voestalpine BÖHLER Edelstahl implementiert: In einem kompakten Gehäuse, das die Sensoren und die Elektronik vor den rauen Umgebungsbedingungen schützt, prüft es direkt neben der Schleifkammer die Oberflächen der vier Knüppelseiten mit einer Genauigkeit von 50 Mikrometern bei einer Geschwindigkeit von 24 Metern pro Minute.
Die Ergebnisse werden auf einem Bildschirm deutlich erkennbar angezeigt. Mithilfe dieses Assistenzsystems müssen die Mitarbeiter:innen den Prüfstand nun nicht mehr für die zeitintensive optische Inspektion verlassen. Das erleichtert nicht nur den betreffenden Personen die Arbeit, sondern ermöglicht darüber hinaus eine bessere Ausnutzung der Maschinen, da nun kein Stillstand der Schleifanlage während der Prüftätigkeit erforderlich ist. „Die Mitarbeiter:innen waren bei der Entwicklung bereits stark eingebunden und sind jetzt dabei, das System zu nutzen und weiterzuentwickeln“, berichtet Betriebsleiter Peter Markiewicz.
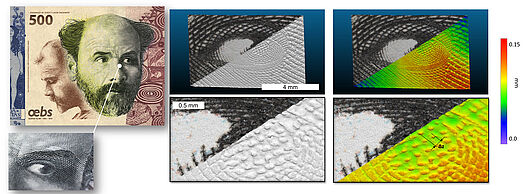
© AIT/Testbanknote mit freundlicher Genehmigung der OEBS
Die Ergebnisse des Scans einer Testbanknote mit dem Konterfei des Malers Gustav Klimt, die von der Oesterreichische Banknoten und Sicherheitsdruck GmbH (OEBS) bereitgestellt wurde: So ist beispielsweise der Stichtiefdruck auf dem Augapfel bei einer gemessenen Tiefe von 57 µm gut zu sehen.
Kleinste Details, ganz groß
Ein anderer Eisatzbereich moderner ICI-Technologien ist die Prüfung von Banknoten: Hier zähen Technologien des AIT seit vielen Jahren zur Weltspitze, um gebrauchte Geldscheine auf Verunreinigungen, Abnützungsspuren oder gar Fälschungen zu prüfen. Die Methoden werden immer weiter verfeinert: Nun wurde ein Mikroskopie-System entwickelt, das die Lichtfeld- und Photometriemethoden mit einer speziellen Projektionsoptik zur Erzeugung eines Parallaxeneffekts vereint: Um eine stereoskopische 3D-Topologie zu berechnen, wird eine Reihe von Bildern aufgenommen, während ein Objekt durch das Sichtfeld der Kamera verschoben wird. Zusammen mit innovativen Bildverarbeitungs-Algorithmen liefert das System hochauflösende 3D-Bilder bei hohen Geschwindigkeiten. Im Fall von Banknoten können Prüfgeschwindigkeiten von 12 mm/s bei einer Tiefenauflösung von 2,8 μm und einer lateralen Abtastung von 700 nm/Pixel erreicht werden – was für die Inspektion in der hochpräzisen Fertigungsindustrie geeignet ist.
Wie gut dieses System in der Praxis funktioniert, wurde bei einem Projekt gemeinsam mit der OEBS (Oesterreichische Banknoten und Sicherheitsdruck GmbH), einer 100-Prozent-Tochter der Oesterreichischen Nationalbank, in zwei Use Cases gezeigt. Zum einen wurde eine von OEBS bereitgestellte Testdruckplatte mit Gräben unterschiedlicher Tiefe von 350 µm bis hinunter zu 25 µm gescannt. Obwohl die Druckplatte wenig Textur hat, konnte das System die Oberflächenform rekonstruieren.
Zum anderen wurde eine von OEBS bereitgestellte Testbanknote mit dem Konterfei des Malers Gustav Klimt untersucht, die verschiedene Sicherheitsmerkmale aufweist, einschließlich Tiefdruck. Mit einer Geschwindigkeit von 7 mm/s wurde insbesondere der Bereich um das Auge von Klimt abgebildet. Die Höhe des Tiefdrucks auf dem Augapfel konnte mit 57 µm genau gemessen werden. Somit eignet sich dieses System perfekt für die schnelle Sicherheitsüberprüfung sehr kleiner Details. Um zu beweisen, dass das System in der Lage ist, auch mit einer Geschwindigkeit von 12 mm/s zu arbeiten, wurde eine zentrale Linie der Klimt-Banknote, die eine ähnliche Qualität und ähnliche Details aufweist, mit dieser Geschwindigkeit erfasst.
Durch solche Neuentwicklungen werden die Einsatzbereiche von ICI-Methoden zur Qualitätsprüfung und Sicherheitskontrolle stetig erweitert: So wird die Technologie aus dem Hause AIT unter anderem auch in der Elektronikfertigung, bei der Produktion von Photovoltaikpaneelen, in der Batterieherstellung oder im Verpackungsdruck angewendet.
Über das AIT Center für Vision, Automation & Control
Center for Vision, Automation & Control (VAC) am AIT Austrian Institute of Technologie – der größten Research and Technology Organisation (RTO) Österreichs – ist eine Forschungseinheit, die die Möglichkeiten der Automatisierung und Digitalisierung nutzt, um Innovationen für die Industrie zu initiieren und voranzutreiben. Im Fokus steht dabei die gesamte Kette „from sensor to decission“: Dabei geht es um die Erfassung von Informationen durch (bildgebende) Sensorsysteme über die Sensorfusion, die Kombination von physikalisch basierten Modellen mit Konzepten des maschinellen Lernens und der Datenanalyse, die Nutzung dieser Informationen in der Fehlererkennung und -isolation, der Optimierung und Regelung bis hin zu den kognitiven Entscheidungen für autonome Systeme.